CarbonTT – Light.Efficient.
Carbon Truck & Trailer GmbH (“CarbonTT”) is a young technology company with focus on composite materials. CarbonTT’s core areas are the development of components using CAD & simulation, development of assembly & joining processes, development of industrial manufacturing processes for fiber composite components, and series production & assembly of fiber composite components. CarbonTT is a global leader in the development and cost-efficient mass production of complex components.
Since 2015, CarbonTT has been developing and manufacturing structural components made of carbon fiber reinforced plastic (“CFRP”) specifically for light commercial vehicles up to 3.5-ton gross vehicle weight. These vehicles have a particularly poor CO2 balance – but due to the rapid increase in online trade, their sales are rising sharply. CFRP lightweight construction is an effective way of increasing the economy of 3.5-ton trucks while at the same time reducing fuel consumption and CO2 emissions. In electric vans, CFRP lightweighting increases the range and increases the payload by compensating for the battery weight.
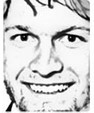
“We make vehicles lighter. So you can carry more payload. And consume less fuel. Additionally, we were able to incorporate other advantages into our products, such as accessible installation space without cross-members or better crash behavior.””
Hauke, Team Lead CAD/CAE
Specifically, three different ultra-lightweight models were developed: based on the Volkswagen T6, the StreetScooter Work L and the Mercedes-Benz Sprinter. In each case, coupons and components were tested, component tests (Hydropuls) and corrosion tests were carried out (climate change test), dynamic driver tests and fatigue tests (bad road test) were run, among other things. CarbonTT implemented the entire process – from initial sketch to portotypes to series components – on its own responsibility.
CarbonTT – Durable.Sustainable.
Various innovations and patents support our company. The latest innovation brought a decisive advantage in production: a unique process allows multiaxial scrims to be fed to the pultrusion plant without wrinkles at high speeds. There, in turn, a proprietary injection box ensures fast, process-safe impregnation of the fibers. The resin is also a proprietary composition of basic materials and additives, in particular to improve processability and aging behavior.
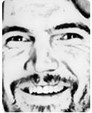
“Process developments are complex, but that’s what makes them so appealing. With great colleagues, we systematically go through the manufacturing parameters and make adjustments. Again and again. But when shiny components are in hand, everything is good.”
Markus, Team Lead Pultrusion
Fiber-reinforced composites (FRP) can be more than just lightweight. While CarbonTT has primarily focused on (continuous, multiaxial) carbon fibers, which have the highest lightweighting potential of all materials, applications are increasingly being developed with recycled carbon fibers, glass fibers or natural fibers (e.g. flax). These fibers have a lower carbon footprint or can even serve as a CO2 sink. In addition, composite components can be a useful reuse of discarded FRP components – for example, wind turbine rotor blades can be given a second life. The new components then use sustainable materials and still offer superior weather resistance and durability.
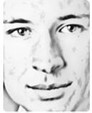
“We are an experienced team from the areas of vehicle construction, aircraft construction and production. Our common motivation is to advance meaningful, sustainable applications.”
Gerret, Band Leader
CarbonTT’s headquarters are in Buxtehude, with a direct link to CFK Valley in Stade, where many innovative companies and institutes with lightweight construction expertise have settled in the Airbus environment. Since 2019, Rheinmetall AG has held a stake of just under 25% in CarbonTT and, as a leading global supplier to the automotive industry, provides support, particularly in the areas of industrialization and sales.